Case Study: Planned Preventative Maintenance
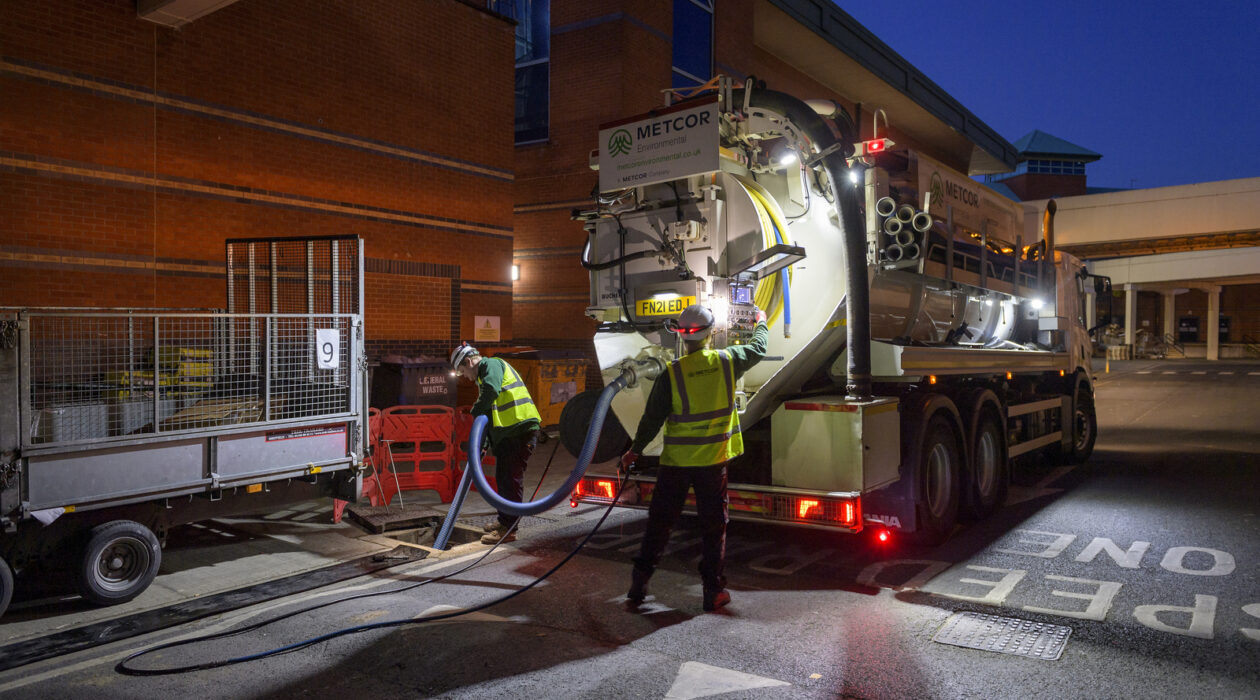
Metcor Environmental provides a PPM service for many sites nationwide for one of Europe’s largest asset managers, who look after or invest in over a trillion pounds worth of property. Their business park by Heathrow is an established centre for modern offices, warehouses and logistics, and it runs 24/7
A routine CCTV survey was conducted for over 500 metres of the underground drainage system, which comprised over 60 access manhole covers. The survey revealed several structural defects, including a steel cable that had punctured the pipework.
The defects were serious enough to warrant immediate remedial action to prevent further deterioration and potential operational disruption at the site.
Metcor Environmental’s team already had a site plan of all the drainage, waste and clean water pipe systems that it had drawn up when they took on the maintenance for the site.
The remedial works were scheduled over two weekday shifts, beginning at 6 PM and concluding at 3 AM the following day. This out-of-hours schedule was chosen to minimise disruption to the business park’s operations.
The CCTV camera system transmits a signal so that an above ground locator can identify the spot underground where the steel cable was jutting into the pipe.
Deployment and Tasks
- The engineers sent in a robotic cutter, also with a camera, via the nearest manhole, which cut the cable into two pieces.
- They then jetted the cable pieces through the pipe system to the nearest manhole, and removed them.
- Having measured and marked the spot where the cable had intruded into the pipe, an inflatable packer was sent through the pipes with a resin patch. When it reached the damaged part of the pipe, it was inflated to the diameter of the pipe, pushing the resin patch outwards, to seal the hole. It was allowed to cure, to harden, for about an hour.
- The pipe was then CCTV survey ed again to ensure the patch had been appropriately applied and repaired the hole left by the steel cable.
Timeline and Completion
The intensive remedial work spanned two full shifts. The team worked diligently through the night to ensure that the drainage system was restored to optimal functionality without affecting the business park’s operations.
“We decided to use this method for repairing the defects because the alternative would have been to dig a 1.5m deep trench to replace or repair the pipework – that would have been far more disruptive to this 24-hour business park, and cost a lot more too. This no-dig solution saved time, money and caused zero business disruption.”
Kyle Claydon, Remedial Drainage Engineer, Metcor Environmental
Client Satisfaction
The client expressed satisfaction with the prompt and efficient handling of the drainage issues. The proactive approach and professionalism of the Metcor Environmental team were key factors in preventing potential disruptions and maintaining the smooth operation of the business park.
________________________________________
This case study showcases Metcor Environmental’s capability to respond swiftly and effectively to critical infrastructure issues, highlighting their expertise in managing complex drainage challenges for major property fund management companies.
Planned Preventative Maintenance programme did exactly what it is supposed to do:
Catch a problem before it caused disruption to this 24/7 modern industrial complex, saving time and money, with a no-dig solution