Leisure
Case Study: FOG Block Leading to Pump Station and Repair
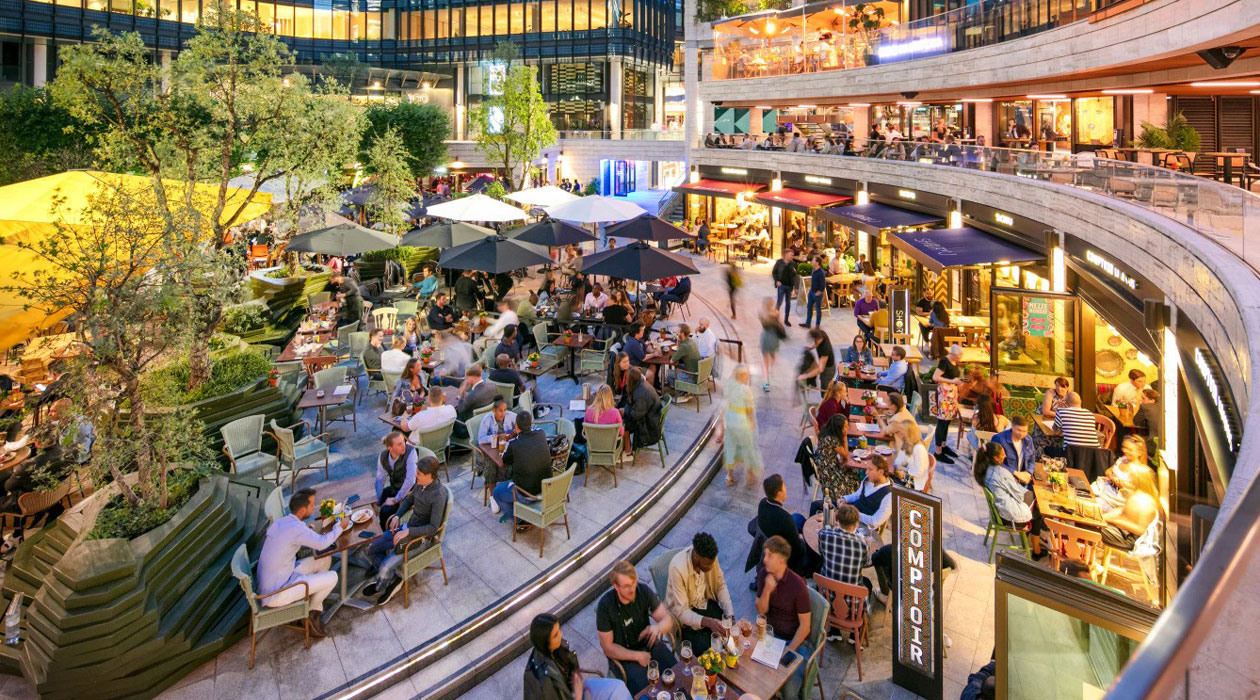
Annually, over ten million people use this very popular retail and hospitality location, so a major challenge was to provide remedials that would not disrupt continuity. The two pump stations had begun to fail, through pipes blocked with fats, oils and grease.
The Challenges:
- The pump stations were underneath an underground delivery yard, busy with daily deliveries and also with construction lorries for a major overhead development.
- There were safety issues from the traffic and from the proximity of a fire exit to one of the pump stations.
- A thorough survey, including cctv, discovered cracking and leaking concrete in the pump pits and the chamber walls.
- Access to the pump stations was restricted via old, heavy, unhinged covers
The Solutions:
Several solutions were considered, including:
- Purchasing and building an above ground temporary pump station
- Bringing in IBC (intermediate bulk container) tanks to make up the operations whilst the pump stations were out of service
The Metcor Environmental Solution:
- Bring in a 4,000-gallon tanker on site in the underground delivery yard
- Cone off pathways for delivery and construction traffic; the tanker and works teams could then operate safely 24/7
- Over-pump from pump stations as required to the tanker, enabling each pump pit to be renovated in turn – laying over 90 metres of hoses between tanker and pump stations
- Replace old access covers with new double door hinged covers
- Disable fire exit by one pump station and build new fire door; access to pump pit would not obstruct fire exit
- Pump pits would be stripped, chambers removed, joins in concrete filled, and a specialised coating applied to concrete walls
- Metcor’s sister company, award-winning Anglo Pumps, would install new Sulzer pumps in both stations, together with inverters to maximise efficiency and sustainability
- Install new electronic control panels
The Result:
- The project ran to schedule, on time
- Two new pumping stations, running at far greater energy efficiency, with new, longer lasting tanks, better protected from leaks.
- No interruption to business at Broadgate Circle
- All specialist materials delivered on time
- No accidents
Metcor Environmental, Anglo Pumps and Aylesford Electrical are all part of the Metcor Group
Broadgate Circle
Broadgate Circle, by Liverpool Street Station, hosts over 30 restaurants and bars, and other businesses, surrounded by a 32-acre commercial complex comprising 30,000 office workers. At weekends the space hosts visitors and tourists.
Share on